Stainless Steel Press Fit vs. Traditional Welding: Pros and Cons
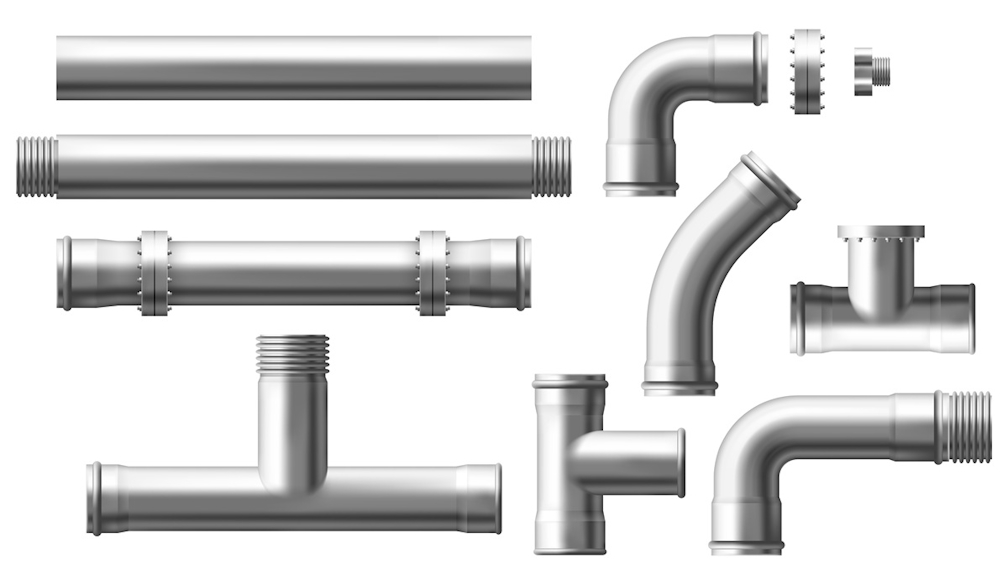
In the world of piping systems, two methods dominate when it comes to connecting pipes: traditional welding and stainless steel press-fit technology.
Welding is the process where extreme heat is applied locally to fuse two pieces of metal together. This is typically done using methods like Metal Inert Gas (MIG) welding or Tungsten Inert Gas (TIG) welding.
In MIG welding, an electric arc forms between a wire electrode and a metal surface, causing them to fuse. In TIG welding, a gas-shrouded arc from a tungsten electrode creates the weld.
Welding can produce highly durable joints, especially when done properly, but it requires significant skill and can be a slow process. The amount of time it takes to complete a weld depends on the material thickness, the type of weld required, the pipe diameter, and the specific conditions of the job site.
On the other hand, stainless steel press fitting is a non-welding method where a battery-powered tool is used to press the pipes and fittings together.
The pressing process creates two types of deformations: radial deformation, which compresses an O-ring in the fitting to ensure a hermetic seal, and geometric deformation, which further ensures that the joint is resistant to slipping and rotation.
A good example of press-fit technology is Europress, a German-manufactured system using hydraulic pressing tools to join pipes. The speed of installation with Europress is notably faster than traditional welding, with some projects seeing up to 10 times faster installation times compared to welded systems.
Comparing Stainless Steel Press Fit to Traditional Welding
Let’s bare the pros and cons of both stainless steel press fit and traditional welding using the following metrics:
Costs
One of the key differences between welding and press-fit technology lies in the cost structure.
Welding is generally considered more affordable in terms of materials, as the materials used for welding (like welding rods and filler materials) are often cheaper than press-fit systems. However, welding projects often require significant labour resources.
Engineers estimate that the overall cost of a welded system is typically split, with ⅓ of the cost going to materials and ⅔ to labour.
On the other hand, press-fit systems tend to have higher material costs, particularly because of the more complex fittings and thicker wall thickness of the pipes. The cost breakdown for press-fit systems is the reverse of welding, with 2/3 of the cost going towards materials and 1/3 towards labour.
However, when you factor in installation time, press-fit systems become more cost-effective. Since press-fit installation is much faster (often taking just seconds per joint) it significantly reduces labour costs. Also, since press-fit systems do not require hot work permits (unlike welding), they can save costs in terms of safety and regulatory requirements.
Installation Time
The speed of installation is where press-fit technology truly stands out. Welding is a time-consuming process. The installation speed depends on several factors, including the thickness of the material, the type of weld required, and the pipe diameter.
Welded connections often require careful preparation, including cleaning, grinding, and preheating the materials before welding. After the welding is done, the joint must be allowed to cool, which adds even more time to the overall installation process.
Press-fit technology, especially systems like Europress, is much faster. The pressing process only takes a few seconds per joint. In fact, some projects using press-fit systems have reduced installation time by up to 10 times compared to welded systems.
Furthermore, because press-fit systems don't require complex setup or the use of heat, they can be installed in environments where welding would be unsafe or impractical. There's also no need to shut down operations for long periods, and this makes it a more efficient choice for ongoing projects.
Durability and Performance
Welding, when done correctly, creates highly durable joints that can withstand significant temperature fluctuations and high pressures.
This makes welding an excellent choice for applications in industries like oil and gas, where high pressure or extreme temperatures are quite common. The welded joints typically last long; they are bound to survive the entire lifespan of the pipe system.
Welding also creates a smooth bore, which is essential for applications requiring high hygiene standards, such as food and beverage transfer systems. The joints are known to provide a very seamless bore that eliminates any potential areas where bacteria could grow.
Press fit fittings are also quite durable, but they offer more flexibility compared to welded joints. The mechanical bond created by the press-fit system is strong enough to withstand vibration, thermal expansion, and other stresses that can occur during installation or normal operation.
While press-fit systems can handle most applications, they are not suitable for high-pressure or hygienic applications, where welding is still preferred.
Nonetheless, press-fit systems typically excel in environments where flexibility and ease of installation are the priorities. They are designed to expand and contract with temperature changes, reducing the risk of leaks over time.
These systems also do not suffer from thermal fatigue, unlike welded systems, which can experience warping or distortion when exposed to heat.
Conclusion
At the end of the day, both welding and press-fit systems have their place in the piping industry. The right choice depends on the specific requirements of your project.
Welding is still the go-to method for high-pressure applications, hygienic systems and situations where you can’t afford to compromise durability, especially if the working conditions of the system are extreme.
And on the other hand, press-fit technology excels in situations where speed, cost-effectiveness and safety matter the most. With its quick installation process, low labour costs, and reliable performance in most conditions, press-fit is becoming an increasingly popular choice for piping systems.