Industries/Site Areas: Ways to Ensure Production At All Times
- Written by News Company
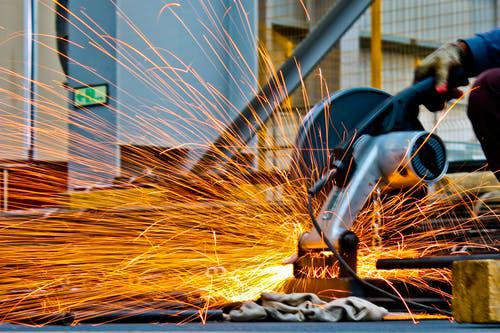
How many hours do you have in a day to work? Quite a few? If you are seeking plans to increase productivity, then you have two choices, either to increase working hours or to start working smartly. Smart working is not a big deal, it all depends on how you manage your work efficiently. If we consider an example of a manufacturing site, this discussion will take you to through a journey on how to effectively utilize your working hours to establish a concept of production at all times. According to a proverb, time is money. If you are a stakeholder of a manufacturing plant then you will understand this concept more easily that what is the reflection of time on money. It is as simple as, more time you invest in your business, more money you make for sustainability.
There is a series of tips and tricks that help us to understand how we can increase productivity and to sustain the model of continuous production. Before going into details, we must establish that there are some value-added benefits for the concept of continuous production for the manufacturing sites. Starting from the basics, effective planning, maintaining a simple process, and many more aspects can be covered in this discussion but we will focus on some of the most important and realistic approaches to ensure worth reading them. If we look into the process of continuous production, some advantages are directly associated with an effective plan of production:
-
Needs and Wants of the Equipment: Every manufacturing organization has a dream to utilize their equipment up to their full capacity but unfortunately none of them can do. The continuous production in manufacturing plants leads the organization to satisfy the needs of the market. One the other hand, installation, and working of the equipment can be a challenge for many but test and tag provides value-added services for the equipment used in the production site.
-
Time Management: In the manufacturing industry, time is the most important aspect to consider. The effective production plan is directly associated with good time management that will help the organization deliver orders timely resulting is exceptional service and quality products. Nevertheless, if the organization can deliver orders timely, it will help them to save their time effectively.
-
Production Cost: In the world full of opportunities, a reduction in business cost can help the organization to multiply its net profit and one possible way to achieve it is to do continuous production or manufacturing. Continuous production can help the organization to utilize resources more efficiently eventually reducing the business cost.
-
Inventory Control: Regular production needs a good amount of inventory to fulfill the needs of manufacturing. If we consider that the organization has the rule of continuous manufacturing then inventory has to be maintained. One advantage of regular production is that the organization will have amazing control over their inflow of raw material and outflow of the end product.
After the discussion of advantages, let's jump on the main theme that is, the most significant, impactful and generating ways for continuous production:
-
Production Workflow: First and the foremost step to consider is to identify the major points that become the barrier for continuous production. With the help of this analysis, the organization will have a checklist that is core pain points of the organization. This checklist can be utilized to evaluate the controllable and uncontrollable aspects of the workflow. Based on these aspects priorities can be suggested to ensure that the organization is stepping towards the vision of production at all times. The most important thing to focus at this point is the impact of changing the methodology of production. If the impact of this change is significant only then it is better to opt for the concept of continuous production. There are chances that the process may become difficult to proceed but the result will be fascinating.
-
Manufacturing Tools And Types Of Equipment: In the manufacturing plants, one of the core elements that need regular maintenance and upgradations are the tools and types of equipment used in manufacturing. Somehow, it is not the process that has to be changed every time, it can be the equipment that needs to be upgraded to scale up the manufacturing process. At this point, an interesting thing is that you need to evaluate which equipment can be most beneficial for the overall process as replacing all the equipment is not feasible anyhow. Apart from the performance of the equipment, the capacity of the tool is also an important aspect to be considered. One of the biggest mistakes many organizations do while replacing old equipment is that they do not consider the aspect of market demand due to which the organizations fail as new machines are not beneficial if the market is saturated and you do not have demand.
-
Structured Workflow and Protocols to Follow: The manufacturing industry has always been complaining about the loss of resources and working hours. One key factor to enhance production is to ensure that every employee of the organization is following protocols and processes defined by the organization. This can only be possible if the workflow is highly organized and employees are assigned with the task of their expertise. Structured protocols of the manufacturing plant can move the organization one step forward to achieve the milestone of production at all times. Somehow, proper allocation of resources and establishing the concept of time-bound working hours can help as a whole.
Conclusion: At the end of the day, we need to understand that maintaining continuous manufacturing is not that easy. It takes a lot of effort and dedication to transform the conventional process of manufacturing to the concept of production at all times. If we claim that the manufacturing industry is the most collaborative business industry around the globe, it may not be false. Collaborative actions have a significant impact on the overall quality of the product as it involves taking help from people who are experts in their respective fields. Everyone moving towards the same goal eventually end up achieving the milestone.