Key Factors to Consider When Buying Industrial Sheds
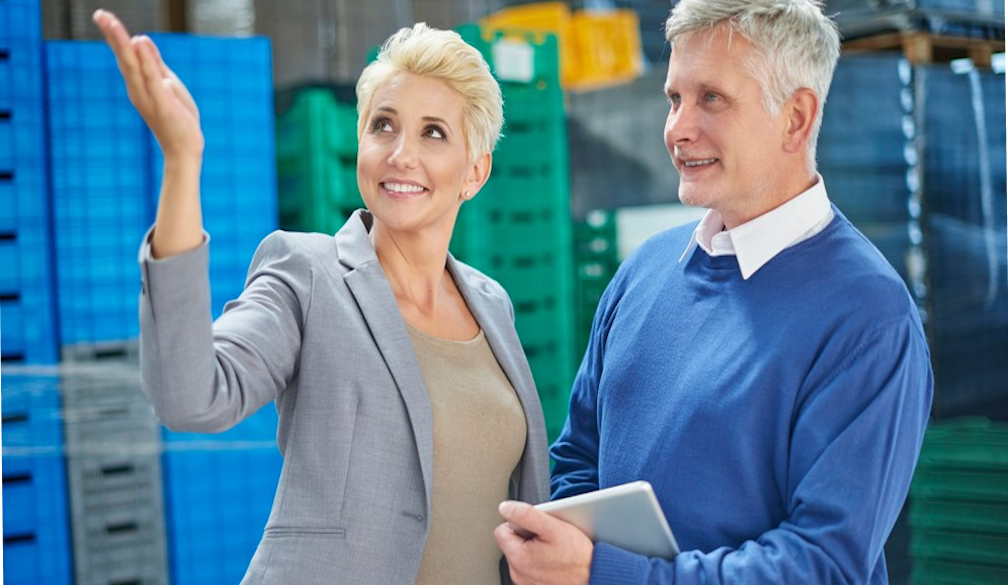
Industrial sheds are pivotal structures in various sectors, including manufacturing, warehousing, and agriculture. Choosing the right industrial shed is a critical decision that impacts operational efficiency, storage capacity, and overall business functionality. Here are the key factors to consider when buying industrial sheds:
1. Purpose and Usage
Understanding Requirements: The primary consideration is the intended use of the shed. Different industries have varied requirements, such as storage, manufacturing, or distribution. Clearly defining the purpose helps in selecting the appropriate size, design, and features.
Customisation Needs: Some businesses may need customisations like specific door sizes for machinery, ventilation systems, or temperature control. Identifying these needs upfront ensures the shed meets all operational requirements.
2. Location and Accessibility
Proximity to Key Areas: The shed’s location should be strategically chosen for easy access to suppliers, customers, and transportation networks. Proximity to highways, ports, and railways can significantly impact logistics efficiency.
Zoning and Regulations: Ensure the selected location complies with local zoning laws and regulations. Check for any restrictions that might affect the shed’s usage or expansion possibilities in the future.
3. Size and Space Requirements
Current and Future Needs: Evaluate both current and anticipated future space requirements. Overestimating can lead to unnecessary costs, while underestimating may result in the need for additional structures sooner than expected.
Layout Planning: Consider the internal layout for efficient workflow. Plan for adequate space for machinery, inventory, employee areas, and potential future expansions. Proper layout planning can optimise operational efficiency and safety.
4. Structural Integrity and Material Quality
Durability and Strength: Industrial sheds should be built with high-quality materials to withstand heavy usage and adverse weather conditions. Steel is a popular choice due to its durability and low maintenance needs.
Environmental Considerations: Assess the environmental impact of materials used. Opt for eco-friendly and sustainable options where possible. Consider insulation and energy efficiency features to reduce operational costs and environmental footprint.
5. Cost and Budget
Initial Costs: Determine your budget and understand the total cost of purchasing and installing the shed. This includes the price of the shed itself, transportation, installation, and any required customisations.
Long-term Costs: Consider long-term maintenance and operational costs. High-quality, durable materials might have a higher upfront cost but can save money on repairs and replacements over time. Energy-efficient designs can also reduce utility bills.
6. Compliance and Safety Standards
Building Codes and Standards: Ensure the shed complies with all relevant building codes and industry standards. This includes structural integrity, fire safety, and environmental regulations. Non-compliance can lead to legal issues and costly modifications.
Health and Safety: Prioritise the health and safety of employees by ensuring the shed design includes necessary safety features. Adequate ventilation, lighting, and safe access points are critical to maintaining a safe working environment.
7. Vendor Reputation and Support
Vendor Reliability: Choose a reputable vendor with a proven track record of delivering high-quality industrial sheds. Research customer reviews, ask for references, and verify the vendor’s experience in the industry.
After-Sales Support: Consider the level of after-sales support provided. Reliable vendors offer warranties, maintenance services, and responsive customer support to address any issues that arise post-purchase.
8. Customisation and Flexibility
Adaptability: Look for sheds that offer flexibility in design and usage. Customisable features allow the shed to adapt to changing business needs without requiring significant modifications.
Expansion Capabilities: Consider future expansion possibilities. A modular design can facilitate easy expansions, saving time and costs associated with building new structures.
Conclusion
Investing in an industrial shed is a significant decision that requires careful consideration of various factors. By thoroughly assessing your needs and evaluating options based on purpose, location, size, materials, cost, compliance, vendor reputation, and flexibility, you can ensure the shed you choose will support your business effectively both now and in the future. Make informed choices to achieve the best return on investment and operational efficiency.